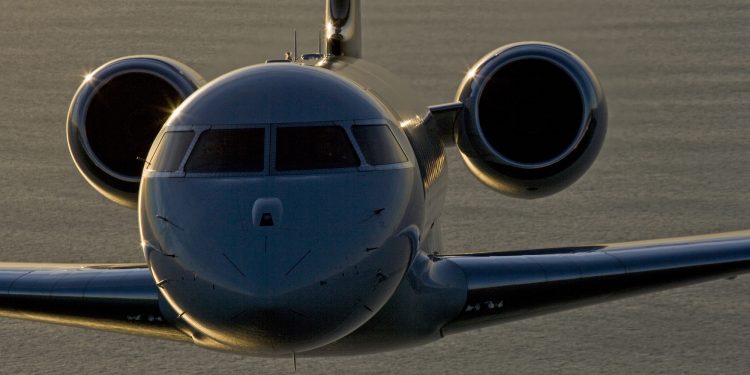
Aircraft manufacturers sponsor researchers who are using stress data from the CNBC to evaluate methods of preventing distortion in thin aluminum parts.
Source: Canadian Neutron Beam Centre (CNBC)
Contact: cnbc@cnl.ca
Image: Bombardier
Boeing once estimated the cost of reworking or scrapping parts with small distortions at about $300 million or more per year. The high cost of not making an airplane part exactly right the first time can be explained by low production volumes over which the high costs of developing new products and ensuring quality are spread. The cost of quality is high because safety and reliability are critical. The cost of developing new parts is also high because trends to minimize weight and optimize performance push the limits of materials—and our knowledge of them.

Thin-walled parts are susceptible to shape distortion.
Not surprisingly, then, parts with slight distortions can be rejected or reworked if they don’t fit properly or if they might not be able to bear the loads required of them. Distortions can be especially frequent in parts with thin walls, such as those used in a plane’s structural frame. That is because machining creates stress near the surface; for a wall that can be as thin as 0.4 millimetres, most of the wall is near the surface, so distortion often results.
To prevent distortions, one solution is to make the walls thicker; however, the increased weight would reduce fuel efficiency and performance. A second solution involves painstaking multiple-step machining processes that drive up the cost.
To find a better solution to the challenge of distortions, Bombardier and the National Research Council of Canada sponsored Professor Jean-François Chatelain’s research team at École de technologie supérieure. Bombardier also provided support for a graduate student to work in both Prof. Chatelain’s lab and at its own industrial facility. The team set out to study how making thin-walled parts from aluminum alloys creates stress, which is a major cause of distortion—and which can be added to by each of many manufacturing processes.
Prof. Chatelain’s team accessed the Canadian Neutron Beam Centre to non-destructively obtain stress data for two ‘work-in-progress’ model parts (i.e., thin-walled parts that replicate those used in large sections of airplane structures). Both work-in-progress parts were made of 7475‑T7351 aluminum alloy. However, the alloy of the first work-in-progress part was made from standard aluminum billets, while the alloy of the second part was made using a special processing recipe to reduce any initial stress.

A graduate student aligns an aluminum sample for stress measurement on the L3 neutron beamline.
Using laser scanning to measure any changes in shape that resulted from the machining, the research team examined the two replica parts before and after machining operations were conducted. The team found the amount of distortion to be directly related to stress from machining measured at the CNBC —and also that the choice of alloy made a big difference. Indeed, the part using the specially made aluminum had much lower levels of stress and distortion.
This research, published in 2012, suggests that rework and scrap might be reduced in thin-walled structural components by focusing on stress reduction and using specially made aluminum that is nearly free from initial stress.
Building on these findings, Prof. Chatelain’s team is continuing to work in partnership with Bombardier to examine the relationship between stress and distortion in parts machined from sheet metal.