Part 2: Managing Continued Risk of Feeder Cracking at Point Lepreau
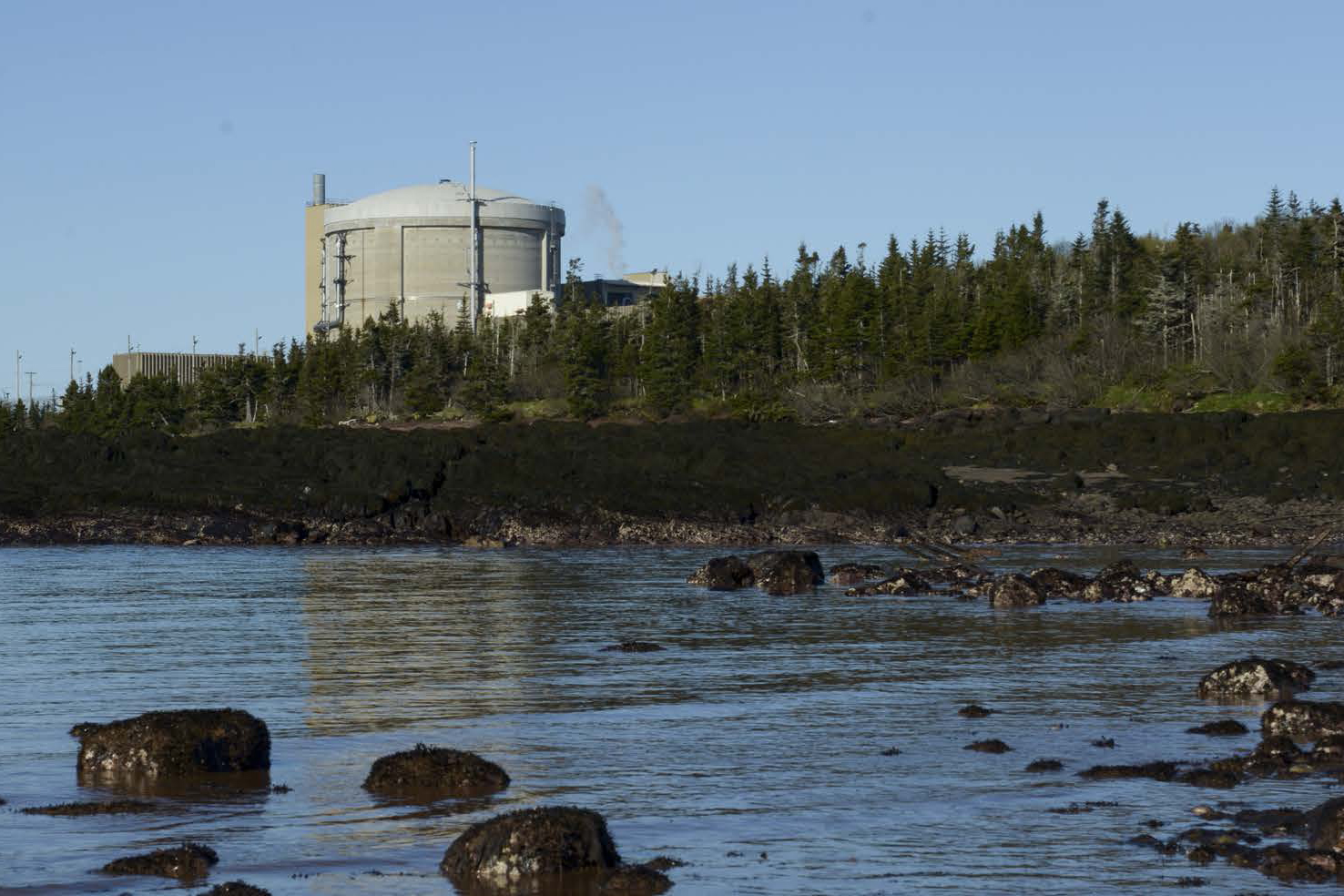
Point Lepreau Nuclear Generating Station. (Image: NB Power)
Stress data from an array of feeder pipes obtained with neutron beams assists NB Power to manage the cracking issues and informs decision-making about the timing of its refurbishment.
Managing the risk of feeder cracking at PLGS from 2001 until its refurbishment in 2008 proved to be challenging for NB Power. On one hand, the cost of many activities to manage the threat was high. On the other hand, the cost of more unexpected outages or extensions of planned outages were also high, especially because of the high cost of replacement electricity. The scale of these challenges is illustrated by the following:
- Feeder degradation was one of two main drivers for the decision to refurbish PLGS three years early.[1] The second life-limiting factor was degradation of the fuel channels. Reducing the 28-year design life of a facility, a $1.4B capital investment,[2] by three years represents a cost impact of at least $6M/yr over 25 years.
- Feeder cracking caused two forced outages (90 days total in 1997 and 2001) and extended three planned outages (13 days total, after 2001) resulting in direct and indirect costs of approximately $60M.
- Before the decision in 2005 to refurbish PLGS, the station’s activities to manage the risk of cracking and maintain adequate safety margins required as much as 5% of the total operations and maintenance budget as of 2005, or roughly $5M/yr.[3],[4]
- Radiation exposure to perform inspection and maintenance on the feeders was about 30% of total outage radiation exposure.[3] Key personnel qualified for these inspections would reach regulatory limits, and thus were not available to perform inspections of other components.[5]
- Feeder cracking made a disproportionate contribution to the total safety risk of PLGS and increased regulatory concern. NB Power reported in 2005 that low margins in the feeders at highest risk and the frequency of cracking had “the potential to increase the probability of consequential feeder rupture and multiple feeder ruptures in the absence of remedial measures. The PLGS Safety Report does not permit design basis events to propagate into further failures.”[3]
- NB Power was challenged by a loss of credibility with stakeholders, including the public, as a result of the recurring cracking.
NB Power developed an economic model to compare strategies to manage the cracking: (1) reliance on leak detection, (2) inspection and repair, and (3) prevention of cracking by performing stress relief or replacing sections of feeder with the highest probability of cracking.[6] As inputs to the model, NB Power needed reliable predictions of how frequently inspections were needed to eliminate surprises and the number of cracked feeders that would be found during the outage inspections.
Because high stresses accelerate crack growth, stress measurements were one factor needed to predict these key parameters. Thus, AECL accessed the CNBC numerous times between 2001 and 2005 to examine stresses thoroughly in various feeder bends of the types found at PLGS, and it used theoretical modelling to corroborate the results.[7] Key outcomes based on the model included:
- A decision to inspect extensively during planned outages rather than to pursue a $10M R&D program to develop prevention methods or to build a safety case based on leak-detection and low safety risk.
- A decision to secure substantial resources to be ready to repair two cracked feeder bends during any yearly outage,[8] thus preventing any unplanned maintenance or outage extension when two cracked feeders were detected in 2006.[9]
- The ability to focus valuable inspection resources at the locations most at risk of cracking.
In retrospect, NB Power’s strategy was effective, since all 10 partial cracks after 2001 were found during planned inspections, and several other pipes with potential for cracks were replaced. All of the cracked bends were consistently found in specific locations of high residual tensile hoop stress that was introduced during bend manufacture,[9] further confirming the importance of stress as a major factor in these material failures. Researchers have concluded that cracking was of the two main modes of feeder degradation at PLGS. The primary drivers of feeder cracking included residual tensile stress,[10] cold work during materials preparation and maintenance, and the in-service temperature.[1]
During the refurbishment of PLGS, which was completed in November 2012, all the feeders were replaced. The materials, preparation methods and maintenance for new feeders were chosen to reduce stress and be less susceptible to feeder wall thinning, and thus feeder cracking is no longer expected to be a life-limiting factor.[1]
Without stress data from the CNBC, NB Power may have had to compensate for a lack of scientific understanding of the cracking by making even more conservative decisions, such as starting the refurbishment prior to 2008, or greatly reducing the operating cycle to facilitate exhaustive inspections, either of which would have come at significantly higher cost.
The next article reviews the impacts on the rest of the industry, and how the CNBC contributed to their responses the concerns of cracking.
Next: Part 3: Assuring Exports, Relicensing of the Reactor Fleet, and Qualification of Innovation
Footnotes
[1] Slade and Gendron. A Last Look At PLGS Life-Limiting Feeder Degradation. 8th CANDU Maintenance Conference. 2008.
[2] Pt. Lepreau had an initial construction cost of $1.4B and was completed in 1983 (Roger Steed. Nuclear Power: In Canada and Beyond. 2006).
[3] John P. Slade, Tracy S. Gendron. Risk-Reduction Strategies used to Manage Cracking of Carbon Steel Primary Coolant Piping at the Point Lepreau Generating Station. 12th International Conference on Environmental Degradation of Materials in Nuclear Power Systems – Water Reactors, Salt Lake City, USA, The Materials, Metals & Materials Society. August 2005.
[4] PLGS’s operations, maintenance and administration budget in 2005 was about $125M. NB Power. 2005-2006 Annual Report. http://www.nbpower.com/html/en/about/publications/annual/NBPAnn_05-06.pdf. However, also note the following reference gives 3% as the on-going cost to the operations and maintenance budget: K. P. Stratton. Life Extension at the Point Lepreau Generating Station – Powering the Future. Proceedings of the International Conference on Opportunities and Challenges for Water Cooled Reactors in the 21st Century. 2009. http://www-pub.iaea.org/MTCD/publications/PDF/P1500_CD_Web/htm/pdf/topic4/4S02_K.%20Stratton.pdf.
[5] K. P. Stratton. Life Extension at the Point Lepreau Generating Station – Powering the Future. Proceedings of the International Conference on Opportunities and Challenges for Water Cooled Reactors in the 21st Century. 2009. http://www-pub.iaea.org/MTCD/publications/PDF/P1500_CD_Web/htm/pdf/topic4/4S02_K.%20Stratton.pdf.
[6] NB Power’s economic assessment of the different life-cycle management strategies was based on assumptions including “the plant had a 10 year remaining life with annual maintenance outages, feeder failure rate of 1.5 per year, a forced outage from a leak would be 30 days, and repairing feeders with cracks found by inspection would extend planned outages by 10 days. For analysis of prevention methods, it was assumed that it would take at least five years and $10M for research, development and implementation.” Other economic inputs, such as maintenance and replacement energy costs are proprietary to NB Power. John P. Slade, Tracy S. Gendron. Risk-Reduction Strategies used to Manage Cracking of Carbon Steel Primary Coolant Piping at the Point Lepreau Generating Station. 12th International Conference on Environmental Degradation of Materials in Nuclear Power Systems – Water Reactors, Salt Lake City, USA, The Materials, Metals & Materials Society, 2005 August.
[7] Yetisir, Donaberger, Rogge. Residual Stresses in CANDU Feeder Bends – Effect of Bend Radius. PVP2006-ICPVT11-93407.
[8] “This contingency included: full training, qualification and mobilisation of repair crews prior to inspection, and repair activities for two feeders in the detailed outage schedule, amounting to approximately six days on the outage duration.” Tracy Gendron, John Slade and Glenn White. Pinpointing cracks. Nuclear Engineering International. January 2007.
[9] Tracy Gendron, John Slade and Glenn White. Pinpointing cracks. Nuclear Engineering International. January 2007.
[10] “It should be noted here that the residual stress is not the only stressor in feeder cracking, but the best known stressor so far. The fact that only one CANDU station out of seven with warm-bent feeder bends had cracked feeder bends indicates that there are other stressors, such as chemistry, local material properties, service-stress, age, etc., contributing to cracking.” Yetisir, Rogge, Donaberger. The effect of manufacturing process on residual stresses of pipe bends. PVP2005-71581.
Series Overview
An unexpected incident at a Canadian nuclear power plant led to an urgent need for greater scientific understanding of the underlying cause. Stress measurements with neutron beams played a critical role, both in the immediate failure analysis and in subsequent activities over a decade to assure the safe, reliable and economic operations of Canada’s nuclear power plants. This series of articles reviews the resulting impacts on the industry, which include informing safety evaluations, providing confidence for a multi-billion export project, minimizing down time, informing lifetime management, and ultimately solving the underlying issue for the long term:
Summary: A Decade of Feeder Studies for Canada’s Nuclear Power Technology
Part 1: Responding to Cracked Feeders at Point Lepreau
Part 2: Managing Risk of Feeder Cracking at Point Lepreau
Part 3: Assuring Exports, Relicensing of the Reactor Fleet, and Qualification of Innovation
Part 4: Maximizing Operating Time and Solving the Cracking Issues Industry-Wide
Mock-up of a CANDU reactor face. The feeders are pipes (black) attached to each end of the hundreds of channels (yellow) through the reactor core holding the nuclear fuel. The feeders circulate heavy-water coolant from the fuel channels to the steam generators. Each feeder contains multiple bends. (Image: NA Engineering)